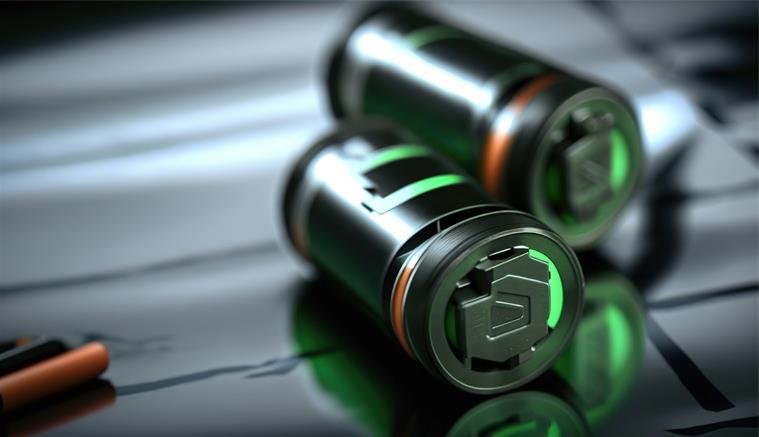
1705
1970-01-01
来源:《粉末冶金材料科学与工程》1999年第三期
编号:CYYJ00248
篇名:温压粉末的制备及其温压行为
作者: 曹顺华 张立华
关键词: 粉末
原文: 粉末冶金是一门集材料冶金与机械制造于一体的新型技术,具有节材、低能耗等显著优点,为机械制造特别是汽车工业提供了大量质优价廉的P/M零件。然而,其中的孔隙决定了零件具有较低的力学性能,限制了P/M零件的使用范围,导致粉末冶金技术与其它零件制造技术相竞争的潜力无法得到充分发挥。为了扩大P/M零件的应用范围,必须提高P/M零件睥密度。目前,用来提高P/M零件密度的常用方法有:高压缩性铁粉的制备与应用;复压复烧;浸铜工艺;粉末锻造;液相烧结;高温烧结。由于这些工艺存在不同程度成本和零件精度难以保证等技术问题,必须寻找新的提高P/M零件密度的技术途径。 温压是1994年由美国霍根纳斯公司在扩散粘结铁粉的基础上开发出来的制备高密度P/M零件的新工艺。至今已申请有关温压的专利20余项,其中涉及到温压用粉末的制备、新型润滑剂、加热装置及相关制备工艺。目前,全球建立了30余条温压零件生产线,能制造出数十种温压零件。温压工艺得到如此迅猛的发展的关键在于其以较低的成本制造高密度P/M结构零件。为高密度零件在性能和成本之间找到了一个较佳的结合点。据报道,温压工艺的相对成本分别比浸铜工艺、复压复烧和粉末锻造工艺降低20%,30%和80%。由于温压工艺制备的压坯强度高、脱模压力和弹性后效低,为制造形状复杂、高精度的P/M结构零件提供了便利。从而,赋予粉末冶金技术较其它零件制造技术以强大的竞争力。 温压粉末是获得高密度铁基P/M零件的技术核心和得以实现的基础。为了促进我国粉末冶金技术的发展和减轻我国P/M零件生产企业对进口温压粉末的依赖程度,中南工业大学粉末冶金国家重点实验室与东风汽车公司、攀枝花钢铁公司合作,在国家“863”计划的资助下,重点放在温压粉末的制备和高密度铁基P/M结构零件的开发上,以建立一整套具有自主产权的、符合中国国情的温压零件制造技术体系。 1 Fe-1.5Ni-0.5Mo温压粉末的制备 Ni,Mo是提高铁基P/M零件力学性能特别是经后续热处理的力学性能的常用合金元素。单质形态的镍、钼在铁中的扩散激能高,在烧结过程能以与铁基发生合金化,形成镍、钼的富集区,达不到提高力学性能的目的。为了使Ni,Mo合金元素与铁合金化,必须提高烧结温度。而在烧结过程中又由于Ni,Mo的扩散和烧结收缩过大,导致零件的精度难以控制。完全合金化粉末的加工硬化速度大和压缩性能又为烧结扩散和零件尺寸稳定性控制创造了条件。目前,我国尚未掌握该技术。 通常,温压粉末的基础原料是雾化铁粉,其市场售价一般在6000到8000元/t,加上其中的合金元素Ni,Mo和聚合物润滑剂,仅原材料成本就高达9000至11000元/t。因而,温压粉末的价格与从国外进口粉末的下限价格接近。这对国内P/M零件制造厂家来说是难以接受的,不利于我国粉末冶金温压成型技术的发展,而必须寻找其它的基础原料来源。 转炉在吹炼过程中产生的烟尘,其中含有20%左右的铁粉。从粒形来看,类似于雾化铁粉。然而,这种铁粉由于杂质含量较高和成型性极差,不可能直接用作粉末冶金用铁粉原料,由于这种铁粉的回收成本仅800元/t左右,故在成本方面具有独特的优势。回收物转炉烟尘铁粉经一系列的处理后,其主要化学成分如下:w(Fe)≥98.4%,w(S)=0.036%,w(C)=0.014%,w(P)=0.169%. 1.1 Fe-1.5Ni-0.5Mo扩散粘结粉末的制备工艺流程 Fe-1.5Ni-0.5Mo温压粉末的制备工艺流程如下:前期处理过的-100目转炉烟尘铁粉经适当选粒后与-200目的镍、钼粉和少量的粘结剂混合均匀。活化处理在该工艺过程中起着关键性作用,即为Ni,Mo合金元素与铁的合金化和使铁颗粒表面的适度粗糙化创造条件。后续退火则具有扩散合金化和使已存在的铁颗粒表面粗糙度保持稳定的功能。 扩散粘结铁粉松装密度为3.13g/cm3,流动性能为27s/50g,添加0.6%硬酯酸锌的粉末在588MPa的压力下进行室温压制,压坯密度为7.16g/cm2。 1.2 新型润滑剂的开发 对于在室温压制情形下的润滑剂如硬脂酸锌主要起润滑模壁的作用,即减小粉末颗粒与模壁间的摩擦力,降低外压损失,有效地提高压坯密度和改善密度分布。而温压用润滑剂的功能则有所不同,除能降低粉末颗粒与模壁间的摩擦外,还能有效地降低粉末颗粒间的摩擦,有利于粉末颗粒在压制过程的旋转和滑动,为颗粒间的相互填充和粉末最大程度的致密化创造条件。而硬脂酸锌在一般的温压温度下已熔化,这不仅造成粉末的流动性大幅度地降低,而且由于硬脂酸锌的结构发生变化而劣化了润滑效果。因此,必须开发新型聚合物润滑剂体系。 1.2.1 聚合物A及其添加量对粉末温压行为的影响 在最初的温压实验时,考察了粉末加热温度对聚合物A添加量为0.6%的粉末温行为的影响,结果如表1所示。表2为聚合物添加量对粉末温压行为的影响。从表中可以看到,温压密度比普通室温压制还低,而且脱模压力大。虽然当添加量为0.7%时,压坯密度有所提高,但弹性后效(0.23%,而其它情形下的弹性后效为0.15%)增大。因此,聚合物A并没有润滑效果,不适合单独作温压用润滑剂。 表1 加热温度对Fe-1.5Ni-0.5Mo粉末温压行为的影响 粉末温度/℃ 100 110 120 130 140 压坯密度/( g.cm-3) 7.04 6.98 6.95 6.94 6.94 脱模压力/MPa 156.8 161.7 265.6 175.7 178.3 表2 聚合物A添加量对Fe-1.5Ni-0.5Mo粉末温压行为的影响 聚合物A的添加量/% 0.5 0.6 0.7 压坯密度/( g.cm-3) 6.96 6.96 7.03 脱模压力/MPa 199.9 196.9 183.7 2.2 聚合物A的改性 据分析,由于聚合物A是一种粘结剂,而必须加入一种使之改性的聚合物B。表2列出的是聚合物A,B的不同配比对温压密度和脱模压力的影响。可以发现,加入聚合物B后压坯密度显著提高而脱模压力迅速下降。其中以10%A+90%B(质量分数)聚合物组合体系作为温压用润滑剂时的温压效果最好,即压坯密度最高,脱模压力最低。所以,温压粉末中聚合物润滑剂选择为10%A+90%B,其添加总量为0.6%。温压粉末的工艺性能:松比3.10g/cm3,流速27.8s/50g;当粉末和模具的加热温度分别为110,130℃时,在86MPa的压力下可获得7.31g/cm3的压坯密度。 表3 聚合物A,B的不同配比下的温压效果 聚合物配比,w(A/B) 60/40 40/60 20/80 10/90 0/100 压坯密度/( g.cm-3) 7.12 7.15 7.26 7.31 7.25 脱模压力/MPa 137.2 134.3 109.7 98.5 115.6 2 Fe-1.5Ni-0.5Mo粉末的温压行为 由于温压效果与工艺参数的选择紧密相关,因此,对于具体的温压用粉末体系,进行温压工艺参数的优化有利于发挥温压在密度上的最大潜力。 2.1 粉末温度 当模具加热温度固定在130℃时,研究了粉末加热温度的变化对粉末温压行为的影响。由图1可以看出,在所有粉末温度的情形下,压坯密度都随着压制压力的增加而增大。当粉末加热温度为90℃时,压坯的弹性后效为0.18%,且在中高压力范围内密度增加速度较快;而当粉末加热温度为120℃时,压坯的弹性效较小,压坯密度增加速度较慢,在相同压力水平下,低压时密度较高。这可能是润滑剂的润滑效果劣化所致;相比之下,当粉末加热温度为110℃时,在中高压水平下,压坯密度最高,脱模压力最低,弹性后效为0.15%。压制压力为735MPa 时,压坯密度为7.35g/cm3。 2.2 润滑剂含量 根据普通室温压制实践,当粉末中润滑剂添加量每降低0.1%,在相同压制压力水平下,压坯密度将增加0.05g/cm3。为挖掘温压的密度潜力,考察了润滑剂添加量(0.5%,0.6%,0.7%)对粉末温压行为的影响。表3是在686MPa的压制压力下的实验结果。从表3中可以发现,当润滑剂含量为0.5%时,不但压坯密度没有增加,反而导致脱模压力增加。这可能是由于润滑剂含量过低使润滑效果降低和外压在压坯上的传递效果下降。而润滑剂含量为0.7%时,虽然脱模压力下降但压坯密度降低,但弹性后效增大。因而,润滑剂的最佳加入量为0.6%,与国外商用温压粉末的润滑剂的添加水平一致。 表4 润滑剂(10%A+90%B)添加量对粉末温压行为的影响 润滑剂添加量/% 压坯密度/( g.cm-3) 脱模压力/MPa 弹性后效/% 0.5 7.26 108.3 0.15 0.6 7.31 98.5 0.15 0.7 7.27 96.7 0.18 注:粉末与模具的加热温度为110,130℃;压制压力为686MPa 3 结论 采用从转炉烟尘回收的铁粉作为制备密度在7.20~7.35g/cm3结构零件的温压铁粉的原料在技术上是可行的;该技术以其成本优势对发展我国特色的温压技术具有一定的促进作用;采用部分预合金化技术制备的Fe-1.5Ni-0.5Mo合金粉末适于用作那些经表面渗碳淬火获得硬化的粉末冶金零件的制造原料。
出处: 《粉末冶金材料科学与工程》1999年第三期
版权与免责声明:
① 凡本网注明"来源:中国粉体网"的所有作品,版权均属于中国粉体网,未经本网授权不得转载、摘编或利用其它方式使用。已获本网授权的作品,应在授权范围内使用,并注明"来源:中国粉体网"。违者本网将追究相关法律责任。
② 本网凡注明"来源:xxx(非本网)"的作品,均转载自其它媒体,转载目的在于传递更多信息,并不代表本网赞同其观点和对其真实性负责,且不承担此类作品侵权行为的直接责任及连带责任。如其他媒体、网站或个人从本网下载使用,必须保留本网注明的"稿件来源",并自负版权等法律责任。
③ 如涉及作品内容、版权等问题,请在作品发表之日起两周内与本网联系,否则视为放弃相关权利。