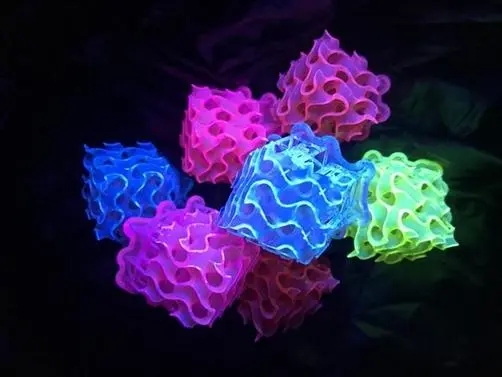
2245
1970-01-01
编号:CYYJ00013
篇名:依靠技术创新,改造传统水泥产业
作者: 韩仲琦
关键词: 粉体 粉体技术 水泥 水泥工业
机构: 天津水泥工业设计研究院
摘要: 水泥,是一种重要的建筑材料,传统的水泥生产从原料采掘到成品出厂,都是散体物料的处理过程,目前已面临着环境,资源和能源的挑战。本文介绍了水泥工业出现的最新粉体技术情况。文章指出,水泥工业可持续发展要依靠创新的粉体技术,综合利用和节约自然资源,降低能耗和其他消耗,减少环境污染,改造传统的水泥产业。
原文: 1.概说 改革开放以来我国水泥工业也有了惊人发展,2001年全国水泥产量约达6亿多吨,连续17年居世界第一位,我国水泥工业最大的技术成就就是新型干法生产技术与装备的不断完善和发展。我国新型干法水泥生产技术所取得的成就归纳起来有如下几点: 开发了一批具有自主知识产权的新技术、新装备,2000t/d生产线的国产化率已达100%,4000t/d已达90%以上;通过技术创新使Φ4×60m窑的生产能力由2000t/d提高到2500t/d,其技术处于国际领先水平;2000~4000t/d生产线热耗与电耗已进入世界先进行列;新型干法的各项经济指标均比开发初期有了大幅度提高,与前几年相比,占地面积下降40~50%,水泥吨投资减少约一半,劳动生产率约提高20~25%;全厂自动化与DCS控制等计算机应用软件已达到或优越于国际水平;已投产的新型干法水泥生产线每年可为国家增加约5000万吨优质水泥,新增产值约150多亿元,节约了引进设备所需的3亿多美元;我国现代水泥行业已具实力,正沿着提高劳动生产率、资源再利用、生态水泥开发及可持续发展的方向更快发展。但目前我国水泥工业也存在着结构不合理的情况,无论在产品结构上还是在技术结构上,我国依然是工艺落后的立窑厂占绝大比例,其工厂数量和水泥产量均占80%左右,而在工厂规模上差距更大,我国平均7万吨/年,而国外先进国家一般都在60万吨/年以上。另外在经济效益、能源与资源的消耗以及对环境的污染方面,我国平均数据都与国外先进水平有很大差距,面临着环境,资源和能源的严重挑战,因此我们必须加快淘汰落后工艺的水泥生产,用新型干法代替和改造立窑、湿法等生产技术,实现结构优化升级,促进我国水泥工业整体提高,用创新技术改造传统水泥产业。 天津水泥院在此关键时刻,深感自己历史责任的重大,确定了“节能、降耗、环境保护和使水泥工业可持续发展”的奋斗目标,并通过技术创新、采用新技术新装备来促进我国新型干法水泥工业有尽快的发展。 2.依靠创新技术改造传统水泥产业 (1)计算机技术的应用和开发 由于计算机在水泥厂的应用,特别是集散型控制(DCS)应用技术的开发,使水泥厂完全改变了传统的生产面貌。 ●应用计算机技术对不同品位矿石搭配开采,保持进厂矿石成分的均匀又使矿山资源得到综合利用,延长了矿山使用寿命。 ●利用计算机生料质量控制系统,可使入磨生料成分均匀稳定,对提高和稳定水泥质量,起到了关键作用。 ●分散控制、集中管理的集散型控制系统(DCS),经过了仪表型和PLC型DCS阶段,技术完全成熟,一个庞大的水泥厂只需几台计算机就可对全厂进行生产和管理控制,使复杂的、难于控制的水泥生产完全实现了自动化。 ●利用成熟的商用网络技术与DCS系统结合,开发的水泥厂生产管理信息系统和全厂管理信息系统,使水泥厂的管理也跃入了现代化,已形成了水泥厂全厂网络化管理。 (2)均化技术的发展和应用 干法生产所以能取代湿法等其他水泥生产方法并能快速发展,就是采用了均化技术,使产品质量得到充分保证。 ●原燃料储存采用均化堆场,原燃料在粉磨前再一次被均化。 ●采用计量精确的块状或粉状物料计量装置。 ●采用X萤光分析仪和高精度计量装置,作到原燃料超前控制,与系统内有关装置组成生料质量控制系统。 ●采用均化系数高的生料均化库。 通过以上均化技术,一方面使水泥质量提高,又可减少或取消物料贮存装置。 (3)粉碎理论的发展与节能粉碎设备的开发 从原料开采到制成水泥要经过原料的破碎与生料的粉磨,以及水泥熟料的粉磨等过程,过去每吨水泥约需130kWh以上的电力,耗能是很大的,然而根据现代粉磨动力学理论,采用新的粉碎设备,使水泥的综合电耗大幅度下降,同时简化了工艺,减少了占地和投资,促进了设备大型化,最终提高了水泥质量和降低了水泥成本。 ●超过40的高破碎比破碎机,能以一段破碎完成从大块石灰石到直接入磨的要求,代替传统的二段破碎成三段破碎,一段破碎已成了水泥厂破碎主要趋势。 ●粉碎机理的研究有了很大进展,根据料床粉碎原理开发出的立式磨(辊磨)和辊压机都大大提高了粉碎效率,生料粉磨采用立式磨是目前主要形式,用立式磨或辊压机作为水泥终粉磨或用立式磨或辊压机与球磨组成预粉磨,都是水泥粉磨的最新形式,因此使用立式磨或辊压机来代替传统的粉碎效率很低的球磨机,在粉碎生料时还可充分利用烧成工序的余热,使水泥的综合电耗可以降到90kWh/t水泥以下。 ●组合式选粉机的出现,将传统的静态和动态选粉机结合在一起,大在提高了选粉效率,并可实现超细选粉,天津水泥院已开发了这种设备。 ●水泥加入细掺合物(如400~800m2/kg的超细矿渣或粉煤灰),可以大量代替水泥熟料,也就减少了石灰石的用量,还可提高水泥后期强度。而超细水泥,是指500~1000m2/kg比表面积,平均粒径2~5μm的产量,这种水泥不单提高了水泥强度,而且减少了混凝土的水泥用量,并提高了水泥浆灌浆性能,天津水泥院开发的超细选粉机可用于细掺合料或超细水泥的生产。 (4)新型干法水泥烧成工艺彻底改变了传统水泥生产方法 ●所谓新型干法,是在传统煅烧水泥熟料的窑尾,连接上垂直向上的几级旋风预热器和一个分解炉,即把回转窑的预热、分解功能几乎全部移出窑外,通过对这一方法的不断优化提高,不单大大降低了烧成热耗,还促进了设备大型化的发展,我国已完成了700~5000t/d国产化水泥装备生产线目前已对10000t/d生产线展开攻关。 ●低压损的5级或6级旋风预热器、利用喷腾、湍流等流场作用的性能优良分解炉、二支承或三支承回转窑、三通道或多通道燃烧器(喷煤嘴)以及最新型空气梁可控流篦冷机等优化匹配,使得烧成热耗可以从每公斤熟料5800~6200kJ降到2926kJ以下,并且燃料燃烧充分,降低了CO2、NOx的排放量,对环境保护起到了很大作用,另外可以使用低热值、低挥发份的燃料或无烟煤,增加了燃料应用的广泛性,降低了烧成成本。天津水泥院已在低挥发煤利用上也取得了好成绩。 ●可以利用窑尾排出的330~380℃废气和篦式冷却机排出的180~250℃废气,通过一种低温换热的废气锅炉去发电,称为中低温余热发电技术,使水泥厂的热能得到充分利用,天津水泥院的水泥厂余热发电技术已用在多家水泥厂。 (5)高环保技术和使水泥工业可持续发展 ●传统的水泥工业产生的有害物质是废气中的粉尘和CO2、SO2、NOx、废水中的有害重金属成分等,当今世界水泥工业的环保技术已达到很高的水平,新建水泥厂的粉尘和某些有害物的排放几乎为零。天津水泥院在防治粉尘、减少CO2、SO2排放等已具有很高技术,大型收尘装置的性能已达到国际水平,现在新的过滤材料不断出现,袋收尘装置的性能将会更好。随着我国落后的小水泥企业逐步被现代化的大型企业所代替,我国的环境污染将会有所改善。 ●我国冶金、煤炭、电力、化工、医药等部门每年排出数亿吨的废渣,此外还有大量有毒有害物质,它们的排放要占用大量土地,还会污染水源、大气。而水泥工业恰恰是可以消化这些废物毒物的工业,通过1450℃水泥回转窑的高温煅烧,一些有毒有害物质可以被处理,一些废渣可以作为水泥的原料或外加剂得以利用,这种水泥叫作环境相容型水泥,天津水泥院已开展了这方面研究。 ●全球气候变暖越来越引起人们的关注,变暖的主要原因是地球上CO2排放量的增加。水泥工业使用的石灰石在煅烧分解时要产生大量的CO2,同时燃料燃烧时也要产生CO2,为此在世界范围内都加强这这方面的研究。在减少石灰石用量的同时,提高利用工业废弃物、城市垃圾和下水污泥等来制造水泥,还要尽可能利用再生能源,如废轮胎、石油焦、废机油、废塑料等,这就叫Recycling,这样的水泥可以叫环境负荷减少型水泥或生态水泥。只有这样水泥工业才能持续发展,天津水泥院已开展了这方面工作。 3.结语 水泥,在相当长的历史时期内,仍是不可代替的建筑材料,然而水泥的加工手段要尽可能达到现代化,我国要尽快以新型干法生产技术代替落后的立窑等传统工艺,抓住机遇、面对挑战、迎头赶上,依靠先进科学技术,围绕产业结构调整和优化,以提高质量、节约资源、节能和环境保护为重点,面向21世纪,把我国水泥工业建成具有国际竞争能力的适应国民经纪发展的现代化原材料产业。 参考文献 1.Hiroshi Uchikawa:Cement and Concrete Industry Orienting Toward Environmental Coad Reduction and Ubste Recycling, chichibu onoda cement comporation,Vol.48, 1997, No.12, 845. 2.中原佳子: 地球环境技术にぉける粉体化学の役割, 粉体工学会志,Vol.35,1998,No.12, 845. 3.我国水泥工业跨世纪发展战略的研究报告,《我国水泥工业发展方向及产品质量标准问题研讨会》资料,1996.11.
版权与免责声明:
① 凡本网注明"来源:中国粉体网"的所有作品,版权均属于中国粉体网,未经本网授权不得转载、摘编或利用其它方式使用。已获本网授权的作品,应在授权范围内使用,并注明"来源:中国粉体网"。违者本网将追究相关法律责任。
② 本网凡注明"来源:xxx(非本网)"的作品,均转载自其它媒体,转载目的在于传递更多信息,并不代表本网赞同其观点和对其真实性负责,且不承担此类作品侵权行为的直接责任及连带责任。如其他媒体、网站或个人从本网下载使用,必须保留本网注明的"稿件来源",并自负版权等法律责任。
③ 如涉及作品内容、版权等问题,请在作品发表之日起两周内与本网联系,否则视为放弃相关权利。