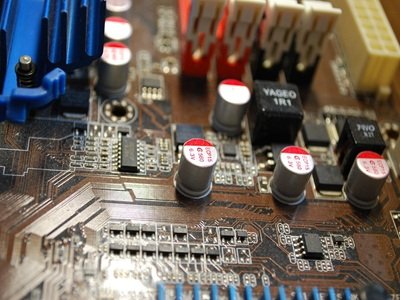
14058
2018-11-05
来源:中国粉体网
中国粉体网讯 为提高三元材料的倍率性能,可将材料一次单晶研磨成纳米级材料,再用喷雾造粒的方法将纳米级三元材料加工成十几微米的二次球团聚体,以改善纳米材料在电池制备过程中的加工性能。该工艺过程所需的设备有搅拌磨、砂磨机、喷雾干燥机。
三元材料喷雾造粒工艺流程图
1—搅拌分散;2—分散浆料泵;3—砂磨机;4—磨后浆料罐;5—造粒送料泵
一、搅拌磨
搅拌磨主要用于三元材料的初步混合与研磨,10μm左右的三元材料经搅拌磨研磨后的粒度能降低到2~5μm。研磨介质一般选择氧化锆球,直径为5mm左右。混合时按一定比例加入纯水、黏结剂和三元材料。若每天的产量定为500kg,则搅拌磨体积选用600L,每批处理量为300L,固含量为30%,每个批次的处理时间为1h左右。
二、卧式砂磨机
砂磨机具有高效分散作用和超细研磨作用,是制备超细研磨、纳米研磨的主要设备。
卧式砂磨机主要组成部分有:主机、研磨桶、循环泵、冷却系统、电器箱、配套连接管路等。
实验室卧式砂磨机示意图
研磨桶分为内桶和外桶,中间带冷却夹层,外桶一般是不锈钢材质;内桶材质可以是金属、氧化锆陶瓷、碳化硅、碳化钨、聚氨酯等。金属材质成本低,但会对产品造成金属污染;氧化锆陶瓷无金属污染,但散热性较差、成本高;碳化硅无金属污染,散热性比陶瓷好,但成本高;碳化钨因为成本很高,目前市场上很少使用;聚氨酯散热性很差。为防止金属污染,三元材料用砂磨机的内衬多采用氧化锆材质。
砂磨机内筒材质优缺点对比表
转子是砂磨机很重要的一部分,可分为盘片式、棒销式、涡轮式等。盘片式多用于分散微米级材料,成本低,剪切力小;棒销式剪切力大,多用于分散纳米级材料;涡轮式用于低黏度物料的纳米级研磨,剪切力比棒销式小,产能稍低。
影响砂磨机工作效率的因素如下:
①砂磨机线速度
线速度越高,传递给珠子的动能就越大,研磨效率就越高。但线速度也不能过高,线速度过高会导致设备温度过高、研磨介质破碎、设备损伤、零件磨损等问题。砂磨机的线速度一般在9~12m·s–1之间,砂磨机真正有效的研磨区域是在研磨盘与桶壁之间的狭小区域,其他部位都是发热区。所以最高效的砂磨机是利用合适的线速度把研磨介质都集中在有效研磨工作区内。
②研磨介质
研磨介质的关键点为研磨介质的密度、直径、填充率。
a.研磨介质密度的影响
不同材质研磨介质的密度各不相同。研磨介质的密度越大,它所获得的能量就越大,撞击力和剪切力也就相应增大,研磨效率就增大,另外,研磨介质与被研磨物料的密度差越大,研磨效果就越好,一般选用锆珠作为研磨介质。
b.研磨介质直径的影响
要获得超细粒径产品需要使用粒径较小的研磨介质。研磨介质直径越小,相同体积内的数量就越多,研磨介质总表面积就越大,研磨介质之间的空隙就越小,因而就具有越大的分散研磨作用面积,并限制了物料的聚集,从而提高分散研磨效率。
c.研磨介质填充率的影响
研磨介质少,研磨效率较低;研磨介质过多,介质和浆料的混合物难以搅动,有“冻结”现象,易在旋转盘上滑动,消耗功率高,研磨效果差,并且易使轴、旋转盘、筒体衬里磨损严重。另外,研磨介质的填充率与物料的黏度,研磨时物料的温度有关,对低黏度溶剂及水性物料而言,充填率可以稍大一些。湿法砂磨机的填充率为70%~80%最为理想。
③冷却系统装置
研磨机都设有冷却系统装置,冷却系统控制研磨机在工作时研磨桶内工作的温度,从而影响研磨介质的填充量和线速度的高低。砂磨机最常出现的问题是机械密封泄漏、堵机、设备温度过高等。机械密封泄漏是目前砂磨机行业内最主要的一个故障,这跟设备的稳定性、精密度、使用材质有关。
三、喷雾干燥
喷雾干燥原理是在干燥塔的顶部导入热风,同时将液料送至塔顶,经过雾化器喷成雾化颗粒,这些颗粒的表面积大,遇高温热风后,水分迅速蒸发,在极短的时间内便成干燥品,从塔底排出,其热风与液滴接触后,温度迅速降低而引起湿度增大,作为废气从排风机排出。废气夹带的颗粒由分离装置收尘器回收。
喷雾干燥塔结构图
1—空气过滤器;2—送风机;3—加热器;4—料浆泵;5—热风分配器;6—喷雾干燥器;7—压缩空气管;8—引风机;9—布袋收尘器;10—蝶阀;11—料仓
版权与免责声明:
① 凡本网注明"来源:中国粉体网"的所有作品,版权均属于中国粉体网,未经本网授权不得转载、摘编或利用其它方式使用。已获本网授权的作品,应在授权范围内使用,并注明"来源:中国粉体网"。违者本网将追究相关法律责任。
② 本网凡注明"来源:xxx(非本网)"的作品,均转载自其它媒体,转载目的在于传递更多信息,并不代表本网赞同其观点和对其真实性负责,且不承担此类作品侵权行为的直接责任及连带责任。如其他媒体、网站或个人从本网下载使用,必须保留本网注明的"稿件来源",并自负版权等法律责任。
③ 如涉及作品内容、版权等问题,请在作品发表之日起两周内与本网联系,否则视为放弃相关权利。