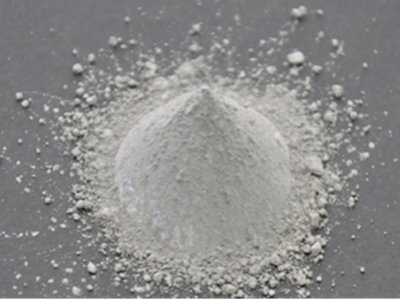
50070
2022-09-05
来源:中国粉体网
中国粉体网讯
1、什么是覆膜砂?
铸造用树脂覆膜砂是指在造型、制芯前砂粒表面覆有一层固态树脂膜的型砂或芯砂,简称覆膜砂。
覆膜砂(图源:长江材料)
2、覆膜砂有何优点?
与粘土砂、水玻璃砂、树脂自硬砂等造型材料相比,覆膜砂具有很多优点:
1)具有优良的流动性,能制作轮廓清晰的复杂砂芯;
2)型芯的表面质量好,致密无疏松,可获得较好的铸件表面质量;
3)溃散性好,有利于铸件清砂;
4)砂芯不容易吸潮;
5)覆膜砂还可以通过选区激光烧结成形,在砂型增材制造中获得了重要应用。
3、影响覆膜砂性能的主要因素有哪些?
影响覆膜砂性能的主要因素有原砂、树脂、固化剂和附加物。
(1)原砂
铸造用原砂主要有硅砂、再生砂、特种砂。
1)原砂粒形:一般圆形为好,因砂粒表面积小,粘结剂加入量少,砂粒间空隙大,有利于通气和排气。
2)集中粒度:三筛分,集中粒度75%~80%为好;四筛分,集中粒度85%~90%为好。由于矿源不同的砂子粒形各异,要求的型砂强度有高有低,透气性、发气量各不相同,要获得合适的性能,需要将砂各目数适当调配,一种粒度配比不可能都适用。
3)硅砂中SiO2的含量高低要求,要根据铸件材质具体情况具体分析。总体来说,如果SiO2的含量过低,则易造成粘砂,导致铸件表面光洁度降低,但热膨胀率低,抗脉纹性好。
硅砂粒度一般使用70/140目、50/100目。树脂在高温时的碳膜隔绝了金属液与砂粒的接触,所以一般不刷涂料也不会粘砂。大型铸件可选用粒度粗一些的硅砂。
4)再生和焙烧硅砂:因高温受热砂粒表面杂质减少,热膨胀率降低(试验证明膨胀率从1.6%降至1.1%),所以其常温和高温抗拉、抗弯蠕变减小,抗脉纹性好。
5)原砂含细粉粒和泥分:细粉和砂粒中粘附的泥分增多会增加粘结剂用量,应严格控制在0.3%以下。
6)人工破碎硅砂严禁覆膜,因形状均为片、尖角形及裂纹(破碎时震动形成),同时砂的表面积大,粘结剂加入量就大。
7)特种砂以人造陶瓷砂为例,人造陶瓷砂为球形,表面光洁度更高,膨胀率均在0.3%~0.6%,应用于覆膜砂工艺时粘结剂加入量少,砂芯蠕变小,应用于单独或掺入硅砂中制造高耐火、高精度的砂芯效果较好。
(2)粘结剂(树脂)
覆膜砂用树脂是热塑性酚醛树脂,对于树脂而言,影响覆膜砂强度的因素有:树脂本身的内聚强度,树脂在砂表面的附着力及润湿性。
树脂内聚强度取决于相对分子的质量,质量越大,内聚强度越高。但随着质量的增大,树脂流动性变差,软化点升高,型砂抗弯强度降低,热膨胀率变小。另外,树脂在覆膜过程中,原砂的加热温度、固化速度(结块)、设备混制的均匀性都直接影响覆膜砂的性能。
(3)固化剂
固化剂是使树脂在热作用下进行固化反应,选择好的固化剂(比如乌洛托品)和确定合适加入量对覆膜砂性能有重要作用。
(4)附加物
为了实现覆膜砂的一些特殊性能要求,在覆膜砂混制时需要加入一些辅助材料,借助这些辅助材料可按需改善覆膜砂性能,比如:
1)如覆膜砂有耐高温需求,则添加含碳物质和防金属液浸透的惰性材料;
2)如需要覆膜砂易溃散,则加入MnO2;
3)如需提高覆膜砂的强度、韧性,则加硅烷、各种酯类、超短玻璃纤维等;
4)如需覆膜砂防粘砂、防脉纹、防橘皮,则加氧化铁、粘土、淀粉等。
4、覆膜砂的工艺应用需注意哪些方面?
根据铸件材质,采取不同的工艺方法,对砂型和砂芯的特殊要求等选择相应的覆膜砂工艺。
(1)制芯工艺
1)芯盒加热温度一般控制在200~260℃,温度低,则加热时间长。砂芯外层的固化厚度只要达到所要求的砂芯强度即可,内部有部分未固化的散砂是允许的。
2)较厚的砂芯,尽量中间掏空制成“壳”芯,既节省用砂,也减少发气量。
3)射砂的压力,应控制在0.5 MPa左右。型芯简单,压力可低一些;复杂、薄壁的铁型覆砂压力要高,可适当增加射嘴和排气塞。
4)加热保温时间视砂芯厚度而定,一般30~200s,要将砂芯烘烤呈褐色,这样既有较高的强度,又能降低发气量和减少存放吸潮性。
(2)各种材质铸件覆膜砂的选用
1)铸钢浇注温度比铸铁高100℃左右,需要有较耐高温的原砂,如SiO2大于96%的硅砂或人造陶瓷砂。
2)铸铁用硅砂的SiO2含量一般为85%~90%,粒度一般为70/140目或50/100目,铸件尺寸小、壁薄宜使用偏细的砂;根据铸件工艺特性,选择普通或有特殊性能要求的覆膜砂,如易溃散、低发气、抗高温蠕度等。
为缓解石英受热膨胀导致砂芯变形、开裂、粘砂,芯砂中可掺入石英相变砂和人造陶瓷砂。
3)铸铝应使用100/200目原砂,因铝液流动性好,细颗粒可避免渗透铝液,若用粗粒度,则必须涂料遮蔽。铸铝使用的覆膜砂必须具备低发气、易溃散等特性。
4)覆膜砂在使用单位必检项目:覆膜砂应按JB/T 8583—2008《铸造用覆膜砂》标准进行生产和检验(用户特殊要求除外),用户如条件所限无法按标准完成全项检查,则必须对表1所列项目进行检查验收。
5、覆膜砂应用中可能出现的问题及其对策
1)如果使用覆膜砂时出现局部一块一块的粘结芯盒,主要是由于树脂覆膜不均造成的。另一个原因就是砂中细粉过多或添加的粉状辅助材料堵塞排气塞,这同样也会导致树脂用量增加造成浪费。
加入粉状物料的覆膜砂,正确混制方法应先加粉料,混合几秒后再加树脂,否则不易混制均匀,还影响覆膜砂整体强度。
2)覆膜砂树脂的耐火度,厚大铸铁件、铸钢件及要求高温浇注的铸件,树脂要具备高的耐火度,在高温下不与砂产生化学反应。因树脂偏碱性对硅的反应更为灵敏,因此,要求原砂有较高的SiO2含量,并适当加碳质耐火辅料,使用陶粒砂、锆砂及喷耐火涂料等。
3)覆膜砂需加热进行固化,芯盒加热位置必须使芯盒受热均匀。射嘴位置要能充分射满空腔,尽量避免射在铸件上,以便清除。排气孔的位置要注意“死角”,离射嘴远的地方需适当多设置排气孔。芯盒要勤清理粘附的砂层,暂不用的模具清理后要涂防锈油保养。
4)覆膜砂的强度要根据砂芯要求而定,过高的强度必然树脂加入量也多,发气量也会增加。
5)砂芯在内腔受热蠕度严重的要使用相变砂、特种砂,并添加各种辅助材料。
6)砂芯薄、细长、四周包围金属液的因芯内高温产生的气体难以排出,一定要使用较粗的原砂,如50/100目、40/70目,外敷涂料(最好用水基涂料),逼迫气体从砂粒空隙中排出。
7)覆膜砂发气量大,而且发气速度慢,在粘土砂型中一定通过芯头把气体引出,否则易出现呛气孔、砂型“放炮”打漏、打破砂型及爆炸性粘砂。
8)较长铸件下部的覆膜砂会过早溃散,无法托起近凝固的铸件,易形成铸件下沉、裂纹,预防措施有以下几点:①快浇,加快冷却,使铸件形成强度;②下型可采用覆砂铁型工艺。
9)叠箱浇注的覆膜砂型壳,一定要在制型时延长烘烤时间,减少发气量,否则由于金属液自下而上充型,将气体都赶到上面,由于气压原因最上几层容易造成呛火和浇不足。
10)覆砂铁型是在金属型内腔表面覆挂一层覆膜砂,厚度为4~20 mm,用砂的厚度调节金属液的冷却速度,铸件壁厚较大的部位砂层宜薄一些,铸件壁厚较薄的部位砂层宜厚一些。因砂型刚性好,浇出的铸件尺寸较精确。由于铁型良好的导热性,金属液冷却的速度快,自补缩性较好,可少用冒口或不用冒口,工艺出品率提高,铸件致密性强,力学性能也会提高。
6、覆膜砂旧砂再生利用
在粘土砂型中使用的覆膜砂芯,浇注后经破碎砂处理可代替新砂使用,壳型覆膜砂则应回收再生利用,砂受热后膨胀率显著降低,再次覆膜树脂加入量会减少。当一个企业日用砂量在10 t以上时,完全可以投资再生覆膜。
覆膜砂旧砂回收再生目前主要有3种方法:(1)热法,将砂加到800℃左右,燃烧掉树脂膜;(2)机械再生,用多级磨擦,酌减至1.6%以下,每次覆膜再加入5%~10%的新砂;(3)用开箱后铸件的余热在震动槽上反复燃烧加热,再经简单磨擦除尘即可。
资料来源:
张江等:覆膜砂在铸造生产中的应用,山东省机械设计研究院、山东省铸造协会等
杨慧:原砂及树脂加入量对覆膜砂性能的影响,江苏省铸造协会
(中国粉体网编辑整理/平安)
注:图片非商业用途,存在侵权告知删除!
版权与免责声明:
① 凡本网注明"来源:中国粉体网"的所有作品,版权均属于中国粉体网,未经本网授权不得转载、摘编或利用其它方式使用。已获本网授权的作品,应在授权范围内使用,并注明"来源:中国粉体网"。违者本网将追究相关法律责任。
② 本网凡注明"来源:xxx(非本网)"的作品,均转载自其它媒体,转载目的在于传递更多信息,并不代表本网赞同其观点和对其真实性负责,且不承担此类作品侵权行为的直接责任及连带责任。如其他媒体、网站或个人从本网下载使用,必须保留本网注明的"稿件来源",并自负版权等法律责任。
③ 如涉及作品内容、版权等问题,请在作品发表之日起两周内与本网联系,否则视为放弃相关权利。