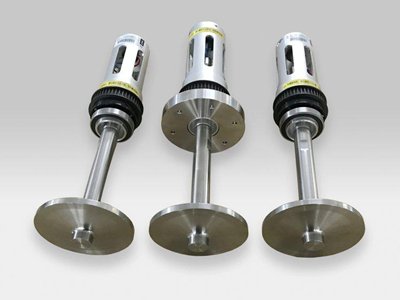
40401
2023-06-08
来源:中国粉体网
中国粉体网讯 同样是烧,焙烧、煅烧、烧结、灼烧有何不同?
来源:pixabay
焙烧
焙烧是将矿石、精矿在空气、氯气、氢气、甲烷、一氧化碳或二氧化碳等气流中不加或配加一定物料,加热至低于炉料熔点的温度,发生氧化、还原或其他化学变化的过程。
焙烧大多为后续的熔炼或浸出等主要冶炼作业做准备,因而在冶炼流程中常常作为炉料准备工序。此外,焙烧有时也可以作为金属矿物精炼的过程。焙烧过程根据反应性质可分为氧化焙烧、还原焙烧、硫酸化焙烧、挥发焙烧、氯化焙烧等。
氧化焙烧
氧化焙烧在焙烧操作中应用最为广泛,是指在氧化气氛中温度低于焙烧物料熔点对原料进行处理,目的是把金属元素氧化为金属氧化物,同时除去易挥发的砷、锑、硒、碲等杂质(若砷、锑、硒、碲是目标产物的核心元素,这种将矿石在空气中加热,使提取对象变为挥发性氧化物呈气态分离出来的方法叫做挥发焙烧),以便后续处理,并把矿石中的硫元素转化为二氧化硫等物质,用于工业生产硫酸或生产亚硫酸盐制备造纸厂蒸煮液等。
还原焙烧
还原焙烧是指将氧化矿预热至一定温度,然后用还原性气体(含CO、H2、CH4等)或粉煤、焦炭等还原矿物中部分或全部高价金属的过程。例如重晶石制取钡盐经典的预处理方法是在碳或无烟煤的作用下于回转炉中进行还原焙烧,使重晶石中的主要成分硫酸钡转化为水溶性的硫化钡(俗称黑灰),再进一步加工为各种钡盐产品。此外,也可用氢气、甲烷、天然气等还原性气体代替煤粉进行还原焙烧,在悬浮炉中还原重晶石,该法可强化还原过程。
氯化焙烧
氯化焙烧是指借助氯化剂(可用氯气、HCl等气体作氯化剂,也可用CaCl2、NaCl、MgCl2、FeCl3等固体作氯化剂,固体氯化剂在氯化焙烧过程中会全部或大部分转化成氯气或HCl等气体氯化剂再起作用)使物料中某些组分转变为气态或凝聚态的氯化物,从而与其他组分分离。
氯化培烧法在矿业、冶金、化工等领域均有广泛应用。通常,矿石中的金属硫化物、氧化物等在一定条件下都可与化学活性很强的氯发生反应,生成的金属氯化物具有熔点低、易挥发、溶解性好、易被还原等特点,因此工业上往往借助氯化焙烧来有效实现金属的分离、富集、提取与精炼等目的。
煅烧
煅烧是指将物料在低于熔点的适当温度下加热,使其分解并除去所含结晶水、二氧化碳或二氧化硫等挥发性物质的过程,所以煅烧过程的反应物通常是固体,生成物是另一种固体和气体。
煅烧作业可用于直接处理矿物原料以适于后续工艺要求,也可用以化学选矿后期处理而制取化学精矿,满足用户对产品的要求。煅烧具体分类如下:
分解矿石:如石灰石化学加工制成氧化钙,同时制得二氧化碳气体;
活化矿石:目的在于改变矿石结构,使其易于分解,例如膨润土微波活化;
脱除杂质:脱除有机物和吸附水等,如高岭土脱羟基、脱碳等;
晶型转化:如二氧化钛、分子筛等焙烧。
烧结
烧结是指把粉状物料转变为致密体的过程,是粉末冶金、陶瓷、耐火材料、超高温材料等工业生产的重要工序。通常在固相化学矿物中配加其他氧化剂或还原剂,并添加助熔剂,在高于炉料熔点的适当温度下发生化学反应并促使其结块。
例如,铬铁尖晶石的熔点很高,加入钠盐可以显著降低其熔点,便于熔融结块。且在有钠盐存在的条件下,稳定的铬铁矿极易被氧化,有助于转化为易溶于水的铬酸钠熔块,烧结后的铬铁矿具有强度高、粒度均匀、高温电阻率大等优势,可以有效节约能源、改善炉料透气性等。
灼烧
将固体物质加热到高温以达到脱水、分解或除去挥发性杂质、有机物和铵盐等目的的操作称为灼烧。灼烧通常指的是实验室里对固体进行的高温操作,加热仪器有酒精灯、煤气灯或电炉等,如海带提碘实验中通过灼烧除去有机物,大学实验室里还常用到电加热套、管式炉和马弗炉等。
小结
对于工业生产中常用的煅烧、焙烧、灼烧,他们的区别不在于温度,而在于一定温度条件下变化的种类。烧结是物料在熔融状态下的化学转化,目的是将物料结块,便于后续操作;焙烧和煅烧是在低于炉料熔点的高温下进行炉料处理的过程,其中焙烧指的是原料与空气、氯气、氢气等气体或添加剂发生化学反应,而煅烧仅是通过高温使物质发生分解,是一种固体生成另一种固体和若干种气体的过程。
参考资料:
苑凌云等.基于高考化学主观题浅议“焙烧、煅烧、烧结与灼烧”
邵建兵.煅烧(焙烧)装备技术在非金属行业的应用和发展趋势
科能达检测选矿科技中心.煅烧、焙烧、灼烧的区别?
(中国粉体网编辑整理/黑金)
注:图片非商业用途,存在侵权告知删除!
版权与免责声明:
① 凡本网注明"来源:中国粉体网"的所有作品,版权均属于中国粉体网,未经本网授权不得转载、摘编或利用其它方式使用。已获本网授权的作品,应在授权范围内使用,并注明"来源:中国粉体网"。违者本网将追究相关法律责任。
② 本网凡注明"来源:xxx(非本网)"的作品,均转载自其它媒体,转载目的在于传递更多信息,并不代表本网赞同其观点和对其真实性负责,且不承担此类作品侵权行为的直接责任及连带责任。如其他媒体、网站或个人从本网下载使用,必须保留本网注明的"稿件来源",并自负版权等法律责任。
③ 如涉及作品内容、版权等问题,请在作品发表之日起两周内与本网联系,否则视为放弃相关权利。