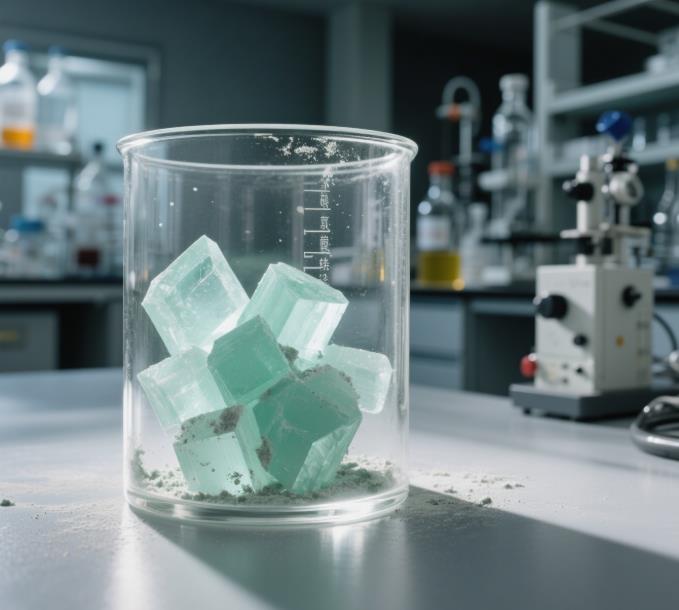
1864
1970-01-01
来源:材料科学与工程
编号:YJHY00003
篇名:温压技术的发展、特点及其技术问题分析(上篇)
作者: 曹顺华 易建宏
关键词: 温压工艺 对策 发展动态
摘要: 本文概述了温压的发展动态及其技术特点;详尽分析了涵盖温压的技术问题,并提出了开发符合国情的温压技术的对策。
原文: 粉末冶金具有节材、低能耗等显著优点。进入八十年代以来,汽车工业比以往任何时候更加依赖于粉末冶金技术,即尽可能多地采用粉末冶金(P/M)零部件以提高其汽车特别是轿车在市场中地竞争能力。然而,P/M零部件地密度是左右其在轿车上应用水平地关键因素。因此,为扩大P/M零部件在轿车上地应用范围,必须提高其密度以获得力学性能优异地粉末冶金零部件。目前,常用来提高P/M零部件密度地技术途径包括:1、高压缩性铁粉地制备与应用;2、复压复烧,即二次压制、烧结工艺;3、浸铜工艺;4、高温烧结工艺;5、粉末热锻工艺。由于这些工艺存在着不同程度地成本和零件尺寸精度保证困难等技术问题,使本富于竞争力的P/M零件难以得到充分发挥。为此,必须寻找新的提高P/M零件密度的技术途径。 一、温压技术的发展: 八十年代末,Hoeganaes 公司的Musella等人在本公司的ANCORBOND工艺即扩散粘结铁粉制备工艺的研究基础上开发出一种所谓温压(Warm Compaction)的新工艺,即ANCORDENSE工艺,并于1990年取得了第一项采用一次压制烧结工艺制备高密度铁基P/M零件的美国专利。通常,模具和粉末原料均需加热,即模具温度为150℃,粉末原料温度为130℃。经温压后,P/M零件的密度增幅为0.15~0.30g/cm3。1992年,Hoeganaes 公司的Rutz和Luk又获得一项美国专利,他们的研究成果标志着温压技术迈向了实用阶段。在1994年、1995年、1996年国际粉末冶金学术年会上发表了近20篇有关温压技术的论文。如瑞典和美国的Hoeganaes 公司,加拿大魁北克金属粉末有限公司等都较系统地开展了有关温压技术的研究。已制备出极限拉伸强度达1500MPa的烧结态铁基P/M零件。在温压过程中,温度的升高使粉末的流动性大幅度下降,为实现压制过程自动化,开展了新型高分子聚合物作为润滑剂的研究,并取得了两项专利。与此同时,Hoeganaes 公司与德国的Linde公司、美国的辛辛那提公司密切合作,研制出温压加热装置,并得了专利。目前,瑞典Hoeganaes 公司,美国Hoeganaes 公司和宾夕法尼亚Pressed metals 公司,瑞士SinterwerkeAG公司,加拿大魁北克金属粉末有限公司,台湾保来得公司等已建立二十多条温压生产线,并能制造出30余种密度在7.25~7.60g/cm3的高密度铁基P/M零件,如电动工具用螺旋齿轮,轿车刹车定位螺母等。Ford汽车公司已将重达1.2kg的温压流体变速涡轮毂用在发动机上,仅此一件就大幅度的提高了铁基P/M零件在汽车上的应用水平。据美国粉末工业联合会执行主席White称,到1996年底,美国轿车中铁基P/M和应用水平已达到13.6kg/辆。Ford公司的目标是到2000年轿车中P/M零件的应用水平将达到22.7kg/辆,这在很大程度上得益于温压工艺的出现。Hoeganaes 公司也因在温压工艺方面的开创性成就而荣获1996年度MPR最高荣誉奖。 相对而言,国内起步较晚,除扬州保来得粉末冶金公司和宁波东睦粉末冶金公司已从境外引进温压工艺生产线外,还没有系统地开展对温压工艺的研究。1995年,北京科技大学和武钢合作开展了采用温压工艺制备高密度粉末冶金磁性材料的研究,现已取得有价值的阶段性成果。中南工大粉末冶金国家重点实验室早在1995年就成立了温压工艺研究小组,其目标是开发出符合国情的温压工艺及温压加热装备。正在开发的温压用粉末原料的工艺性能与Hoeganaes 公司和魁北克金属粉末有限公司的原料接近。目前该实验室与东风汽车公司联合开发采用温压工艺制造高密度铁基P/M轿车零件的研究项目,已得到国家“863”计划的资助。相信,该项目的开展将有助于加快我国开发温压工艺的步伐。 二、温压工艺的技术特点: 温压工艺被誉为“开创粉末冶金零件应用新纪元的一项新型制造技术”,其关键在于以较低的成本制造出高性能的铁基P/M零件,为轿车用零部件在性能与成本之间找到了一个较佳的结合点。据资料分析,虽然温压工艺比常规一次压制烧结工艺的相对成分提高了20%,但比浸铜工艺,复压复烧工艺,粉末热锻工艺分别降低20%,30%和80%。除此以外,温压工艺还具有自身独特技术优点: 1、压坯密度和烧结密度高。采用温压工艺,通常可获得7.25~7.60g/cm3的铁基P/M零件。在同一压制压力下,比一次压制烧结工艺的密度提高0.15~0.30g/cm3。相应的,获得相同密度所需的压制压力降低140MPAa左右,这为较低吨位粉末压机压制大尺寸中密度铁基P/M零件创造了条件,相对地增大了压机的吨位。 2、压坯强度高。在相同密度水平下,经温压的压坯,其强度是常规压制压坯的1.25~2.0倍。这一特点为粉末冶金工艺制造形状复杂的机械零件提供了方便,也提高了粉末冶金技术与其它零件制造竞争的能力。一方面,普通压制烧结工艺由于其压坯强度低,在脱模过程中很容易导致形状复杂压坯的破坏,从而无法成形。然而,温压工艺克服了这一缺点。另一方面根据粉末冶金技术和压机工作特点,垂直于压制方向的P/M零件侧面形状特征是不可能成形的,如横向孔等。采用温压工艺后,由于压坯强度高,可在烧结工序之前直接对压坯进行机加工,节约机加工工时和提高刀具的使用寿命。 3、脱模压力低。温压工艺的脱模压力比普通压制工艺降低30%以上。低的脱模压力意味着温压工艺易于压制形状复杂的铁基P/M零件和减少模具磨损从而延长其使用寿命。同时,还可以降低粉末料中润滑剂的添加量,进一步提高压坯密度。因为,润滑剂每降低0.1%,压坯密度将增加0.05g/cm3。 4、弹性后效小。烧结后零件尺寸变化比普通压制要低得多,如Distaloy AE基材粉末经温压后的烧结收缩接近于零,易于获得高尺寸精度的铁基P/M零件。 5、当零件密度、材质相同时,采用温压工艺制得的材料极限抗拉强度比复压复烧工艺所制得的材料提高10%左右,而疲劳强度提高了10~40%。特别是,零件经温压、烧结后进行适度的复压,其疲劳性能与粉末热锻件相当。这些力学性能指标达到了轿车发动机,传动及刹车装置的使用性能的要求,可望为连杆的制造提供一条可行的技术途径。 6、压坯密度分布均匀。采用温压工艺制备齿轮类零件时齿部与根部间的密度差比常规压制工艺低0.1~0.2g/cm3。 由于这些特点,在国际粉末冶金学界,人们称温压工艺是导致粉末冶金技术革命的一项新技术。
出处: 材料科学与工程
版权与免责声明:
① 凡本网注明"来源:中国粉体网"的所有作品,版权均属于中国粉体网,未经本网授权不得转载、摘编或利用其它方式使用。已获本网授权的作品,应在授权范围内使用,并注明"来源:中国粉体网"。违者本网将追究相关法律责任。
② 本网凡注明"来源:xxx(非本网)"的作品,均转载自其它媒体,转载目的在于传递更多信息,并不代表本网赞同其观点和对其真实性负责,且不承担此类作品侵权行为的直接责任及连带责任。如其他媒体、网站或个人从本网下载使用,必须保留本网注明的"稿件来源",并自负版权等法律责任。
③ 如涉及作品内容、版权等问题,请在作品发表之日起两周内与本网联系,否则视为放弃相关权利。