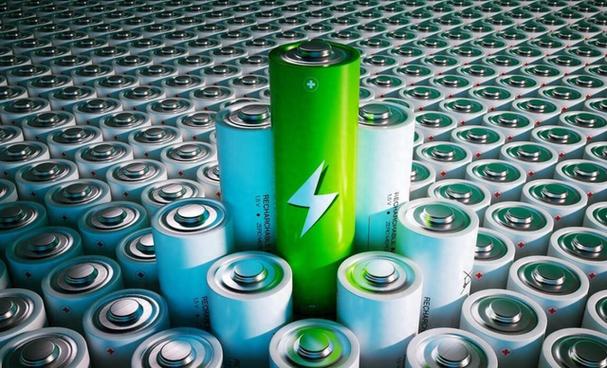
2160
1970-01-01
编号:TCHY00021
篇名:日用陶瓷制品等静压成型用粉料的工艺性能
关键词: 等静压成型 日用陶瓷粉料 工艺性能 坯体质量
摘要: 本文分析了日用陶瓷制品的等静压成型过程,并详细论述了所用日用陶瓷粉料的工艺性能。
原文: 1、前言 日用陶瓷制品的等静压成型完全摒弃了陶瓷泥料的可塑成型方式,不需消耗石膏模具,自动化程度高,坯体形状尺寸精确,表面光洁,致密度高,机械强度好和产品质量高,坯体成型后便可直接进入修坯工序等,从而简化了日用陶瓷制品的生产工序,减少了生产场地及热源消耗等。因此20世纪90年代初,我国湖南醴陵、江西景德镇、重庆、福建德化及河北唐山等地先后从德国内奇公司(NETZSCH)及多尔斯特公司(DORST)引进了20多台(套)日用陶瓷制品等静压成型生产设备和生产技术,投入实践生产中取得了令人瞩目的经济效益。即使如此,大多数用户仅了解日用陶瓷制品等静压成型用陶瓷粉料——日用陶瓷粉料的一些基本常识,对其缺乏系统而全面的认识。因此在实践生产中,日用陶瓷粉料的某些重要工艺性能往往被人们所忽视,结果造成日用陶瓷坯体产生严重的压制裂纹等成型缺陷以及等静压成型机模具的严重粘模或破损等。所以说积极研究和探讨日用陶瓷制品的等静压成型过程及日用陶瓷粉料的构成,并努力改善日用陶瓷粉料的工艺性能,对于提高日用陶瓷制品的产品质量及企业的经济效益等具有深远而重要的意义。 2、等静压成型过程 日用陶瓷制品的等静压成型就是帕斯卡定律在日用陶瓷制品成型方法上的科学应用。其具体成型过程如图1所示,静模是成型盘、碟类日用陶瓷制品的凹面,它是在凸形静模基体上浇注一层耐磨塑料膜;动模则是成型盘、碟类日用陶瓷制品的盘底面,它是在动模的凹面上安装一个与盘、碟类日用陶瓷制品形状相似的耐磨塑料软膜,并将此耐磨塑料软膜固定和密封于动模上。结果动、静模贴紧时,其空腔就形成了一个比盘、碟类日用陶瓷坯体体积约大1倍多的空间,施加适宜的合模压力后,日用陶瓷粉料迅速填满此空腔并关闭填料口,最后向动模进油口通入高压油,高压油将迫使耐磨塑料软膜向静模方向移动并挤压日用陶瓷粉料,因此日用陶瓷粉料在结合剂等作用下将压制成均匀致密的盘、碟类日用陶瓷坯体,这就是盘、碟类日用陶瓷制品的等静压成型过程。 由此可见,盘、碟类日用陶瓷制品的等静压成型过程实质上就是在适宜的等静压成型制度的作用下,日用陶瓷粉料各组分颗粒的相互移近靠拢以致变形等,迫使其孔隙率的减少和日用陶瓷坯体的结构致密化的过程。 3、日用陶瓷粉料的组成 盘、碟类日用陶瓷制品之所以能够等静压成型是由于用于等静压成型的日用陶瓷粉料含有一定量的塑性物料(如粘土和结合剂等)以及适量的瘠性物料(如石英或方石英等),否则它就不能压实成型,成不了盘、碟类日用陶瓷坯体。同时为了降低日用陶瓷制品的烧成温度及减少热耗等,通常在其配方中又加入适量的助熔剂(如长石等)由此可见,日用陶瓷粉料是由石英、长石和粘土等颗粒以及分布在这些颗粒之间和毛细孔中的水分和气体所组成的混合物。 4、日用陶瓷粉料的工艺性能 虽然日用陶瓷粉料的制备方法很多,但目前国内外普遍采用陶瓷泥浆喷雾干燥以制备颗粒级别较多、级配又合理的近似球状颗粒的日用陶瓷粉料,并且具有良好的工艺性能,有利于获得高质量的盘、碟类日用陶瓷坯体。 4.1 颗粒级别及其级配比例 颗粒级别即颗粒的大小,通常由其线性尺寸——粒径来描述。虽然粒度?粒径?的测定方法很多,但由于日用陶瓷粉料的颗粒较粗,因此我们通常采用最为简单的筛分法来测定其颗粒级别及其级配比例。 筛分法就是利用筛孔尺寸大小不同的标准套筛测定颗粒级别及其级配比例的方法。具体说来就是让日用陶瓷粉料通过一套筛孔尺寸大小具有一定比例、筛网宽度和筛丝直径都按国家标准制造的筛子组——标准套筛,并且其上层筛孔尺寸较大,下层筛孔尺寸较小,直至最底层。然后称重各筛面的筛上料及筛下料(最底层的筛底料)的重量,据此绘制日用陶瓷粉料颗粒的累积粒度曲线[1],从而确定日用陶瓷粉料的颗粒级别及其级配比例。由于颗粒累积产率50%的平均粒度d50通常决定了日用陶瓷粉料的工艺性能及产品质量[1][2],因此根据颗粒的累积粒度曲线也可以很方便地确定其d50。 如果颗粒尺寸较大,虽然其流动性较好,但所得盘、碟类日用陶瓷坯体表面粗糙;反之,颗粒尺寸较小的微细粉料易于填塞排气通道,造成排气困难,极易产生压制裂纹等成型缺陷。同时根据颗粒的最紧密堆积原理可知,采用同一规格尺寸的颗粒紧密堆积时,其孔隙率高达45%[3];而采用50%的粗颗粒,10%中颗粒和40%的细颗粒紧密堆积时,其孔隙率可降低至22%[3];显然采用颗粒级别更多及级配更合理的颗粒紧密堆积时,其孔隙率还会降低;也就是说由此所成型的盘、碟类日用陶瓷坯体的致密度及机械强度等更高、产品质量更好。那么人们自然会问,日用陶瓷粉料如何选用其颗粒级别及其级配比例呢?目前,国内外盘、碟类日用陶瓷制品等静压成型生产经验表明:日用陶瓷粉料通常采用:0.5一0.4——0.315一0.2一0.16—0.1一0.05mm 即28—32—42—60—80一150—230目[2][4] 规格的标准套筛(国家标准套筛)检测和控制日用陶瓷粉料的颗粒级别及其级配比例,并且其累积产率50%时的平均粒度d50。应为260μm<d50。<320μm[2][4],而粒度小于100μm的细颗粒应小于 4%[2][4]及粒度大于 500μm的粗颗粒也应小于6%[2][4]。 4.2颗粒形状 目前,国内外日用陶瓷粉料普遍采用陶瓷泥浆喷雾干燥制备近似球状颗粒,易于迅速填满形状复杂的型腔并获得较高的填料密度,从而确保形成致密度高而机械强度好的盘、碟类日用陶瓷坯体。 4.3 粉料含水率 日用陶瓷粉料的含水率在很大程度上影响颗粒的结合强度及等静压成型机模具的粘模等。显然,日用陶瓷粉料的含水率较低,有利于延缓等静压成型机模具的粘模时间,减少抹模次数;虽然此时颗粒的结合强度较差,但我们可以通过加入适量的结合剂来提高日用陶瓷粉料的结合能力。另一方面,由于陶瓷泥浆喷雾干燥制粉的热耗较大,并且盘、碟类日用陶瓷制品等静压成型时的工作环境也具有一定的湿度等决定了日用陶瓷粉料的含水率又不能太低。因此,目前国内外日用陶瓷粉的最佳含水率为:1.5~3%[2][4][5]。 4.4 粉料容重 日用陶瓷粉料的容重是指陶瓷粉料颗粒在重力的作用下填满单位体积容器所具有的重量。它主要与陶瓷泥浆的含水率、粘度、配方及泥浆的雾化压力等参数有关。显然日用陶瓷粉料的容重越大,其颗粒堆积越紧密,那么所得盘、碟类日用陶瓷坯体的机械强度及致密度等就越高;否则,日用陶瓷粉料的容重越小,其颗粒堆积还不够紧密,由此等静压成型的盘、碟类日用陶瓷坯体的机械强度及致密度等必将较低。因此国内外盘、碟类日用陶瓷制品等静压成型所用日用陶瓷粉料的容重如下: 长石瓷及滑石瓷:840~1000克/升[2][4](0.84~1克/厘米3? 骨质瓷:940~l020克/升[2][4](0.94~1.02克/厘米3) 4.5 粉料流动性 陶瓷泥浆喷雾干燥制备的日用陶瓷粉料通常为近似球状的颗粒,具有较好的流动性和填料密度,能极大限度地缩短盘、碟类日用陶瓷制品的等静压成型时间,从而提高劳动生产率。目前,日用陶瓷粉料流动性的测量,通常是让日用陶瓷粉料填满一量筒(量筒直径必须适宜,通常不小于6毫米[1][2]?,通过测定日用陶瓷粉料的填料时间便可确定其流动性[1][2]。 4.6 粉料硬度 日用陶瓷粉料必须具有一定的硬度,才有利于日用陶瓷粉料颗粒的输送和填料,否则日用陶瓷粉料颗粒在输送和填料等过程中就会自行破碎,从而影响日用陶瓷粉料颗粒级别及其级配比例等。但日用陶瓷粉料颗粒也不能过硬,以致阻碍其变形而压实成为盘,碟类日用陶瓷坯体。 4.7 粉料的压缩比 即使日用陶瓷粉料是由陶瓷泥浆喷雾干燥制备的颗粒级别较多级配比例又合理的近似球状颗粒,但它们达到最紧密堆积时仍具有一定的孔隙[2][3],因此日用陶瓷粉料颗粒之间总会形成一定的孔隙并具有一定的压缩性。事实上,日用陶瓷粉料的压缩比就是填料型腔体积与所得日用陶瓷坯体的体积之比,它是盘、碟类日用陶瓷制品等静压成型模具设计的前提。目前,国内外盘、碟类日用陶瓷制品等静压成型生产经验表明:采用陶瓷泥浆喷雾干燥制备的日用陶瓷粉料的压缩比通常大于 2[5]。 4.8 粉料的粘模 在盘、碟类日用陶瓷制品的等静压成型生产过程中,由于日用陶瓷粉料与等静压成型机模具(耐磨塑料膜)频繁摩擦,因此在日用陶瓷坯体与等静压成型机模具表面之间总会形成一定强度的吸附膜[6],如果此时附膜的剪切强度大于日用陶瓷坯体的剪切强度,那么日用陶瓷坯体脱模时,等静压成型机模具表面将粘附陶瓷粉料团块[6],严重影响日用陶瓷坯体的质量,这就是等静压成型机模具的粘模。 等静压成型机模具的粘模主要取决于日用陶瓷粉料的配方、含水率、颗粒级别及其级配比例、添加剂(结合剂及减水剂等)的种类和用量,耐磨塑料膜的材质、表面硬度及其表面光洁度以及盘、碟类日用陶瓷制品等静压成型生产工艺制度等因素。等静压成型机模具一旦粘模,等静压成型机将被迫停机抹模,严重降低了等静压成型机的实际生产能力及产品质量。造成原材料的浪费及增大操作工人的劳动强度等。因此积极研究并减弱日用陶瓷粉料的粘模能力,有利于提高盘、碟类日用陶瓷制品的产品质量。 4.9 其它工艺性能 日用陶瓷粉料的其它工艺性能,诸如日用陶瓷粉料颗粒的结合强度、变形、韧性和加工硬化能力等对盘、碟类日用陶瓷制品的等静压成型过程也有一定的影响,但这些工艺性能指标目前还难于测定[2][7],因此实践生产中对颗粒的结合强度、变形、韧性和加工硬化能力等尚未加以严格控制,一般是通过在其坯料配方中加人适宜的结合剂和稀释剂(减水剂)等以弥补其缺陷[2][7],达到提高日用陶瓷坯体的致密度和机械强度等目的。 5 坯体质量 日用陶瓷粉料工艺性能的好坏,最终表现为等静压成型所得日用陶瓷坯体的质量及制品焙烧后的产品质量等,日用陶瓷坯体的质量主要表现为:表面质量、压制裂纹等成型缺陷、坯体的致密度及断裂强度等。 5.1 表面质量 坯体的表面质量主要是指同一批产品,其坯体形状尺寸的精确性并且其表面平滑光洁、无凹坑、无气泡、无斑点等缺陷。坯体的表面质量主要是由日用陶瓷粉料的颗粒级别,级配比例以及等静压成型机模具的材质、表面硬度及表面粗糙度等决定的。显然表面光洁及硬度较高的等静压成型机模具与日用陶瓷粉料频繁接触时所形成的吸附膜的剪切强度较低[6],不易粘模,易获得表面质量较高的日用陶瓷坯体。同时含有适量细颗粒的日用陶瓷粉料又易于填满复杂型腔的各角落,有利于改善日用陶瓷坯体的表面质量。 5.2 压制裂纹等成型缺陷 日用陶瓷粉料在等静压成型过程中,由于日用陶瓷粉料颗粒受力后将产生一定的弹性变形和塑性变形,塑性变形又将导致颗粒的加工硬化及其弹性极限的提高等[2][7],因此刚成型的盘、碟类日用陶瓷坯体内积蓄了一定的弹性应变能,这种弹性应变能在等静压成型压力去除后,却企图通过弹性膨胀释放出来,使其内应力在一定程度上得到消除,这就是等静压。 成型日用陶瓷坯体的弹性后效作用[2][7],并表现为成型后的坯体尺寸大于其型腔模具的相应尺寸。由此可见,正是由于日用陶瓷坯体的弹性后效作用,致使盘,碟类日用陶瓷制品卧式等静压成型后能自动脱模,达到缩短等静压成型周期及提高劳动生产率的目的。另一方面,日用陶瓷坯体的弹性后效作用也是形成压制裂纹的主要原因,压制裂纹通常潜伏在日用陶瓷坯体内,直到焙烧后才暴露出来,严重时才表现为可见裂纹、因此实践生产中,我们通常通过控制等静压的泄压速度等,确保盘、碟类日用陶瓷坯体的弹性后效作用发生的过程尽量缓慢而均匀,避免产生压制裂纹等成型缺陷[2][7]。 国内外实践生产经验也表明:盘、碟类日用陶瓷坯体脱模后,其瞬间膨胀量?即弹性后效作用)通常应控制在0.6~1%[2],否则,日用陶瓷坯体就会形成压制裂纹等成型缺陷,严重影响其产品质量。 5.3 坯体致密度 盘、碟类日用陶瓷制品等静压成型所得日用陶瓷坯体的致密度通常应达到其坯体瓷化密度的65~70%[2],否则,不利于修坯及转运工序等。坯体的致密度通常用ρ来描述,并采用称重法进行测定,其具体操作就是:首先称重干燥坯体在空气中的重量G1,然后将此干燥坯体浸入密度为ρ0的煤油中(因煤油的渗透能力特别强,在极短的时间内可使整个日用陶瓷坯体浸湿?,并立即称重它在煤油中的重量G2,那么坯体的致密度近似为:ρ=ρ0??G1/G1-G2?? 5.4 坯体断裂强度 德国对日用陶瓷粉料等静压成型后所得日用陶瓷坯体的断裂强度[2]的测定方法制定了专用标准——DIN51030[2],该标准认为日用陶瓷坯体成型后应立即测量其断裂强度,绝不能用干燥后的日用陶瓷坯体来测量。因为等静压成型的日用陶瓷坯体一旦脱模,由于其含水率仅为1.5~3%[2][4][5],日用陶瓷坯体在极短的时间内干燥过程就会开始,显然在这种情况下所测得的数据并不能如实反映盘、碟类日用陶瓷坯体在等静压成型过程中日用陶瓷粉料的移动和变形等行为[2]。因此实践生产中通常在动模的移动方向采用位移感器测量日用陶瓷坯体的永久变形X及成型压强(成型压力)P,直至日用陶瓷坯体断裂破坏等全过程。然后以永久变形X为横坐标,成型压强P为纵坐标做应力——位移图,即可确定日用陶瓷坯体的断裂强度,如图2所示为某一盘、碟类日用陶瓷坯体的应力——位移图[2]。同时盘、碟类日用陶瓷制品的等静压成型生产经验表明:通过调整等静压成型的泄压速度,可使日用陶瓷坯体的弹性后效发生的过程尽量缓慢而均匀,因此日用陶瓷坯体的弹性后效通常较小仅为0.6~1%[2],所以当外力作用于刚成型的日用陶瓷生坯时,会立即产生塑性变形,毫无疑问此时其应力——位移(变形)是非线性的,这与图2是十分吻合的,从而也充分说明了图2的准确性。 6 结束语 目前,盘、碟类日用陶瓷制品等静压成型用粉料——日用陶瓷粉料的工艺性能是世界各地日用陶瓷制品等静压成型生产厂家及陶瓷工作者共同关注的问题。我们认为通过调整日用陶瓷粉料的配方,控制水和添加剂的加入量,采用陶瓷泥浆喷雾干燥生产技术制备颗粒级别较多、级配较合理的含水率仅为1.5~3%的近似球状颗粒,选用表面硬度较高且表面光洁的等静压成型机模具?耐磨塑料膜?及适宜的等静压成型工艺制度等,能最大限度的缩短等静压成型机模具的粘模时间及减少抹模次数,从而达到提高日用陶瓷制品的产品质量及企业的经济效益等 。 参考文献 [1] 郑水林 编《超细粉碎原理、工艺设备及应用》 中国建材工业出版社1993年5月 [2] A.Geigle,K.Hauswurz, S.Mager,“Optimzation of Spray Dried Gramulates for Isostaic Pressing of Tableware”Interceram Feb,1993. [3] 蔡祖光 “墙地砖坯体的成型压力及其对产品质量的影响”《中国陶瓷工业》 1996年3月 [4] Flatware Press System DORST——NETZSCH Fig.230.10 Operation Instructions [5] 蔡祖光 “日用陶瓷制品的等静压成型” 《陶城报》 2000年5月5日 [6] 蔡祖光 “墙地砖压机模具的粘模及防护”《陶城报》2001年3月2日 [7] 马福康 编《等静压技术》冶金工业出版社 1992年3年
版权与免责声明:
① 凡本网注明"来源:中国粉体网"的所有作品,版权均属于中国粉体网,未经本网授权不得转载、摘编或利用其它方式使用。已获本网授权的作品,应在授权范围内使用,并注明"来源:中国粉体网"。违者本网将追究相关法律责任。
② 本网凡注明"来源:xxx(非本网)"的作品,均转载自其它媒体,转载目的在于传递更多信息,并不代表本网赞同其观点和对其真实性负责,且不承担此类作品侵权行为的直接责任及连带责任。如其他媒体、网站或个人从本网下载使用,必须保留本网注明的"稿件来源",并自负版权等法律责任。
③ 如涉及作品内容、版权等问题,请在作品发表之日起两周内与本网联系,否则视为放弃相关权利。