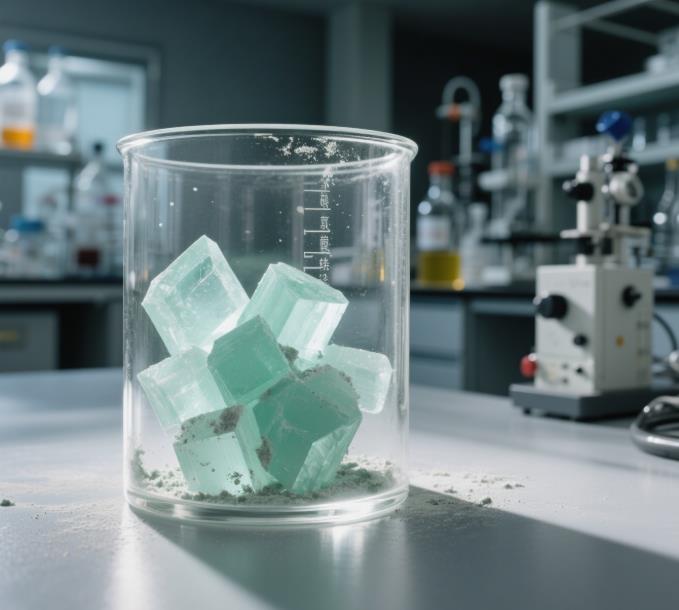
2749
1970-01-01
编号:TCHY00012
篇名:新型陶瓷超细粉料制备方法
原文: 一、传统法 传统法主要是对大块物料应用机械力的方法使其破碎、粉碎。目前大规模粉料制备常采用此方法。机械力包括的范围很广,既可以是粉碎过程中施加的作用力,亦可以是一般的压力和摩擦力,还可以是液体中的空穴作用和气体中冲击波的作用所产生的压力。最常用的设备有球磨机、搅拌磨、行星磨、气流磨、振动磨等。但是简单的机械加工难以获得高性能的超细粉料。球磨物料仅仅用延长时间无法达到超细化,甚至在一定时间后延长球磨时间将导致已细化的物料再团聚而粗化。从粉体机械力化学的角度看,粉碎过程可认为近似于一种可逆的反应过程。 当两个不同方向反应的速度相等时,粉碎过程出现平衡,达到粉碎极限。为了获得超细粉,通常采用两种办法,即粉体表面改性处理和及时分离出超细粉。粉体表面改性处理是增加粉体附加值的有效措施。最常见的方法是通过各种改性剂或偶联剂对无机粉体包覆,使亲水性无机粉体亲油化,从而显著提高粉体的成型性能,如采用热压铸工艺生产氧化铝陶瓷,添加油酸能收到良好效果。 分离超细粉也是提高粉碎效率的有效手段,分离可分为湿法和干法两类。动力可以是水力也可以是风力。目前高效选粉机已有多种形式,有一级、二级、三级选粉装置,能达到使粗颗粒回流,合格的细粉及时得到分离,保证产品粒度、节约能耗的最终目的。经过分级的粉料最大颗粒尺寸可达到微米级,已能满足新型陶瓷中普通产品的使用要求。获得更细粉料是非传统法制备粉料的任务。 二、非传统法 新型陶瓷的性能很大程度上取决于材料的组成及其显微结构,要获得预期显微结构的高性能材料,需要采用高纯、超细、化学成分均一、粒度适宜组成可控的粉末原料。显然传统的制粉技术已无法满足这些要求。近几十年来各种非传统法制备陶瓷粉料的研究十分活跃,国内外均已取得显著成果。其中主要采用化学共沉淀法、溶胶凝胶法,气相沉积法水热法喷雾热分解法等,通过液相制备粉末可获得粒度远小于1μm的颗粒,并且可通过工艺条件的控制,使粒度分布窄小,颗粒多呈球形。由于在液相中可实现分子、离子水平上的均匀混合,因此液相法特别适用于多组分粉料。在非传统法制备超细粉时团聚问题同样应引起足够的重视,严格工艺,采取适宜的表面活性剂就可获得满足如下基本要求的高性能陶瓷粉料。这些基本要求是: (1) 化学成分纯度高,均匀性好。 (2) 相组成准确、均匀。 (3) 粒度<1μm,粒度分布范围窄。 (4) 颗粒形状为球形或自形晶形。 (5) 团聚程度小。 (6) 粉料流动性好。 由于传统的机械磨方法制备的粉料不可能获得细小而分布窄的超细微粉,并且研磨介质的磨损会使原料受到污染,致使粉料质量变差,产品附加值较低。而非传统法虽然成本较高,但粉料性能佳、质量高,相应的产品附加值也高,可获得显著的经济效益。因此,超微粉末制备方法的探索与开发,对于促进新型陶瓷的发展具有重要的实用意义。 非传统法制备粉末是将物料由离子、原子通过成核和生长两个阶段而制成粒子的方法,很易获得1μm以下的微粒,归纳起来,该法主要有液相法和气相法两大类。现择要介绍如下: 1、 化学共沉淀法 这种方法是在含有多种可溶性阳离子的盐溶液中,通过加入沉淀剂(OH-、CO32-、C2O42-、SO42-等)形成不溶性氢氧化物、碳酸盐或草酸盐等的沉淀,然后将溶剂或溶液中原有的阳离子滤出,沉淀物经过分解后即可制得的高纯氧化铝微粉,纯度为99.9%以上,细度为0.1~0.2μm,其它具有化学计量组成的烧结性良好的BaTiO3、PbTiO3、MnFe2O4等粉料均可由此法来制备。化学共沉淀法设备简单,较为经济,便于工业化生产。 2、 溶胶-凝胶法 溶胶-凝胶法是80年代迅速发展起来的新型液相制备法,其制备过程是将所需组成的前驱体配制成混合溶液,再经凝胶化和热处理(干燥和煅烧)。此法广泛用于莫来石、堇青石、氧化铝、氧化锆等氧化物粉末的制备。由于胶体混合时可以使反应物质进行最直接的接触,以达到最彻底的均匀化,所以制得的原料性能相当均匀,具有非常窄的颗粒分布,团聚性小,同时易于控制粉末颗粒尺寸。例如用此法可获得平均粒径为0.4μm的α-Al2O3粉末,粒度为0.1~0.5μm的NaZr2P3O12及0.08~0.15μm的钛酸铝晶相粉末。 3、喷雾热分解法 化学共沉淀法在工艺技术上往往存在胶状物过滤困难,沉淀剂易混入杂质,沉淀过程中会导致各成分的分离或水洗时部分沉淀物重新溶解等问题,为此,开发了溶剂蒸发法,即喷雾法。用喷雾法所得的氧化物粒子为球状,流动性好,易于制粉成型。喷雾法通常有冰冻干燥法、喷雾干燥法和喷雾热分解法三种。 喷雾热分解法是将金属盐溶液喷雾至高温介质气体中,使溶剂蒸发和金属盐受热分解在瞬间发生而获得氧化物粉末。 用本法合成各种复杂氧化物超细粉末,大有发展前途,其应用实例列于表3-1。 4、气相法 采用气相法制备氧化物细粉的方法主要有不发生气相化学反应的蒸发-凝缩法和气相化学反应法两种。 (1)不发生气相化学反应的蒸发-凝缩法 此法是将原料高温加热使之气化,然后用电弧或等离子体火焰的大的温度梯度进行急冷而凝缩成微细粒子。如用电弧加热时,以原料(无导电性时与石墨混合)为阳极,使氧化物在空气中蒸发,金属和碳化物在惰性气体中蒸发。如用等离子流加热有三种形式:①用等离子使火焰直接接触原料;②连续地将原料投入等离子体火焰中;③预先将原料铸成圆筒状,再将等离子体火焰插入圆筒体的空心,使其表面层熔融蒸发。用这些方法可获得5×10-3~10-1μm的细粉,粒子呈球状或近似球状。 (2)气相化学反应法 此法是通过挥发性金属化合物蒸气的化学反应而合成预期物质。气相化学反应法与热分解法和沉淀法相比,有以下几个特征: ① 原料金属化合物有挥发性,易于精制,生成的粉末是高纯度的,且不需粉碎。 ② 生成的粒子很少凝聚。 ③ 易于制得粒径分布范围窄的超细粒子。 ④ 气氛容易控制,除氧化物外,用液相法难以直接合成的金属、氮化物、碳化物、硼化物等非晶质氧化物也可用此法合成。目前,金属氯化物、炭黑、ZnO、TiO2、、SiO2、Sb2O3、Al2O3等细粉已进行工业化生产。高熔点的氮化物和碳化细粉的合成也可应用此法。 由气相反应法生成氧化物粉末三种基本类型是:挥发性金属氯化物的氧化或水解;金属蒸气氧化;金属化合物热分解。 激光合成法是以激光为热源的一种气相合成法。目前,国内外用激光法合成SiC超细粉已获得成功。其制备原理是选用吸收带与激光的激发波长相吻合的反应气体,通过对激光能量的共振吸收和碰撞传热,在瞬间便达到自反应温度并完成反应,物体在高的过饱和度下迅速成核、生长,因物体不吸收激光能量,因而以极快的速率冷却而成为超细粉料。
版权与免责声明:
① 凡本网注明"来源:中国粉体网"的所有作品,版权均属于中国粉体网,未经本网授权不得转载、摘编或利用其它方式使用。已获本网授权的作品,应在授权范围内使用,并注明"来源:中国粉体网"。违者本网将追究相关法律责任。
② 本网凡注明"来源:xxx(非本网)"的作品,均转载自其它媒体,转载目的在于传递更多信息,并不代表本网赞同其观点和对其真实性负责,且不承担此类作品侵权行为的直接责任及连带责任。如其他媒体、网站或个人从本网下载使用,必须保留本网注明的"稿件来源",并自负版权等法律责任。
③ 如涉及作品内容、版权等问题,请在作品发表之日起两周内与本网联系,否则视为放弃相关权利。