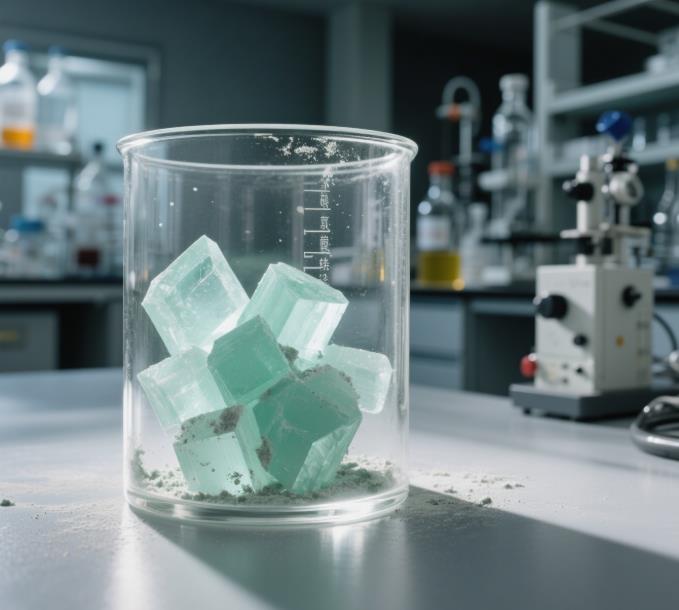
1617
1970-01-01
来源:材料科学与工程
编号:YJHY00005
篇名:温压技术及其致密化机制的研究进展
原文: 【摘 要】 综合评述了国内外温压技术的研究进展,并对其 致密化机制进行了探讨。在此基础上,对今后的研究方向提出了几点建议。 【关键词】 粉末冶金;温压技术;致密化机制 Progress of Research on Warm Compaction and Its Densification Mechanism ZHANG Shuang-yi, LI Yuan-yuan (South China University of Technology, Guangzhou 510641, China) 【Abstract】 The recent development of warm compaction tec hnology at home and abroad is reviewed. Its densification mechanism is also disc ussed. On the basis of that, several directions for the future investigation on warm compaction are suggested. 【Key words】 powder metallurgy; warm compaction; densifi cation mechanism 1 引 言 通过提高粉冶件的密度从而提高其性能是粉末冶金科技工作者长期努力的方向。温压技术因 可将钢铁粉冶件的密度提高0.10~0.25g/cm3,且具有较低的生产成本,而被认为是进 入90年代以来,粉末冶金生产技术方面最为重要的一项技术进步,亦是当今粉末冶金工业的 发展方向之一。研究表明[1-2],假定一次压制/一次烧结的普通粉末冶金工艺的成本为1,则粉末锻造的成本为2.0,复压/复烧的成本为1.5,渗铜工艺的成本为1.4,而Ancordense温压工艺的成本仅为1.25。该技术现已成功地应用于制造高密度、高强度、复杂形状的粉末冶金零件,如链轮、传动齿轮、螺旋齿轮等。目前温压粉冶件在汽车工业中越来 越多的应用已使粉冶件获得了不断扩大的市场份额[1-7]。 因此,本文拟通过介绍温压技术的最新进展,分析其致密化机制和技术关键,从而有助于国 内温压技术的研究工作及其在实际生产中的应用。 2 温压技术研究进展 所谓温压技术即是将混合粉末加热到150℃左右(也有报道为可加热到250℃[8])进 行压制,然后用传统的烧结工艺进行烧结。在压制过程中,可利用传统的压制设备。其工艺 流程如图1所示。 图1 温压工艺过程示意图 1994年,在加拿大多伦多举行的PM2TEC94会议上,美国Hoeganaes公司宣布了其开发的Anc ordense温压工艺。它使用的是该公司的Ancordense预制粉末,并加入新型高温聚合物润滑 剂,经在140℃左右(粘结剂玻璃化温度以上)一次压制后一次烧结就能使密度达到7.25~7.55g/cm3,并使其分布更为均匀,从而提高生坯和烧结体的性能,降低脱模力[1-6 ,9-11]。加拿大Quebec Metal Powders公司也开展了温压工艺的研究工作,考察了包括 模壁润滑剂在内的润滑剂的种类、数量以及温度、压力等因素对粉冶件密度的影响。所选混 合粉成分为: 混合粉A:Atomet 1001+2.5%Ni+0.6%石墨+0.6%润滑剂; 混合粉B:Atomet4401+2.0%Ni+0.6%石墨+0.35%MnS+0.7%润滑剂。 混合粉采用专利合批技术进行粘结剂处理,然后在不同的温度下进行压制,并在1120℃、90 %N2-10%H2气氛中烧结25分钟。研究结果如表1所示[12]。国外其它有关的公 司和科研机构也进行了类似的研究工作[13-17]。 国内对温压技术的研究起步较晚,主要研究单位有北京科技大学、中南工业大学、武汉粉末 冶金公司、上海汽车工业公司和华南理工大学等。有关研究结果表明[18-19]:可 通过调整温压粘结剂的玻璃化温度来降低温压温度;采用无粘结剂温压工艺也可不同程度地 提高生坯密度。文献[19]采用武钢水雾化铁粉和还原铁粉,并配以自制的三种润滑剂,在 517MPa压制压力和130℃、150℃、170℃的温度下分别进行了温压试验,其一次压制/一次烧 结密度最高可达7.22g/cm3。 表1 混合粉A与B的生坯和烧结体性能 压制温度/ ℃ 压力/ MPa 性能 混合粉A 混合粉B 150 690 无空隙密度/(g.cm-3) 7.452 7.378 生坯密度/(g.cm-3) 7.31 7.25 相对密度/%PFD 98.1 98.3 生坯强度/MPa 23.1 22.8 烧结密度/(g.cm-3) 7.33 7.27 121 690 生坯密度/(g.cm-3) 7.27 7.20 相对密度/%PFD 97.6 97.6 烧结密度/(g.cm-3) 7.32 7.26 在教育部和广东省重点科技攻关项目经费的资助下,作者近年来采用粉末冶金方法,研制出 了SiC颗粒增强铁基复合材料,其综合性能较之于普通的钢铁粉末冶金材料有较大的提高[20]。在此基础上,为进一步提高材料性能,采用温压技术制备Al2O3、SiC颗粒 增强铁基复合材料,取得了一定的进展,其研究结果将另行报道。 总的来说,关于温压技术研究还很不充分,且大多都只是局限于工艺研究,研究的成果也都 受到专利保护。至于致密化机制和压制理论方面的研究工作,目前国内外开展得还较少。但 由于温压技术具有很高的技术和商业价值,它已引起了学术界的强烈兴趣。德国Fraunhofer 应用材料研究所从1996年4月开始了对温压技术的基础性研究,其中包括对温压压制过程的 计算机模拟和温压件烧结机制的研究[16]。 3 温压技术的成形理论 3.1 温压技术的致密化机制 一般认为,妨碍获得更高且更均匀生坯密度的主要原因是粉末材料的塑性或可压缩性较差、 内应力和弹性回弹较大、以及压制过程中由于摩擦等原因而不能更为有效和均匀地传递压力。温压技术之所以能提高生坯密度,主要原因就在于它能改善粉末颗粒间及其与模壁间的润滑状况,影响粉末的弹、塑性性质,从而提高粉末的流动性和可压缩性,改善粉末的充填行为,并减少压力损失,提高有效压力。 要改善粉体间及其与模壁间的润滑状况,主要是从粘结剂和润滑剂着手。不过,这里需要明 确粘结剂、润滑剂、聚合物等的概念。因为在不同的文献中,这些概念经常未能加以区分,聚合物既可指粘结剂,亦可指润滑剂。通常,用于温压的预制粉末都会先进行粘结剂处理,目的是在粉末颗粒表面上形成一层均匀的薄膜,以便让粉体在具有防止污染和分层特性的同时,具有良好的流动性和可压缩性。制成预制粉后,使用前再加入润滑剂并混合均匀。温压时,一般将压制温度控制在粘结剂玻璃化温度之上的某一较小的温度范围内(5℃左右[5-6])。此时,粘结剂处于粘流态,可在粉体表面铺展和流动,有利于进一步改善润滑剂的分布,并将其粘附于粉末颗粒表面,从而提高润滑剂的润滑效果。 温压技术要求压制温度应控制在一定的范围之内,因为所选润滑剂在此温度范围内具有最佳 的润滑效果,同时由粘结剂和润滑剂所形成的润滑膜随着温度的过分升高也更容易被破坏。文献[12,13]的实验数据表明:对于不同的聚合物系统,都存在一个最佳的压制温度范围,尽管在实际生产中温度的波动也许会超出这个范围。 温度对粉体材料弹、塑性性质的影响是显然的,由于粉末颗粒可塑性的改善而导致生坯密度 的提高几乎是所有研究者的共同看法[8,22]。不过,这种影响还与粉末材料的成分、制备工艺、形状、粒度及其分布等因素有关。因此,基体材料的成分、物性参数和几何参数等也是开发温压技术用预制粉末时应考虑的重要因素。 3.2 温压技术的成形规律 由于影响粉冶件致密化机制的各种因素都会综合地反映在粉体的成形规律之中,因此,讨论 相关的成形规律是非常必要和有意义的。 此前关于粉体压制成形的理论研究虽然开始得比较早,相关的经验压制方程也比较多[22-25],但都是以常温下的压制过程为研究对象的,其压制理论中都未考虑到温度对压制过程和生坯密度的影响。 果世驹等[21]对温压成形规律进行了唯象分析。在研究中引入了“压制压力强化因子”这一概念,用以描述温度使作用于粉体的压力得到的强化,或对有效压力的提高。试图通过对室温压制方程进行修正而使其适用于温压工艺的情况。其依据是H.G.Rutz[5]的实验结果(压制温度为140℃)和自己利用无粘结剂铁粉温压工艺试验的结果[19]:在某一压制压力下,温压生坯的密度比室温压制生坯的密度高,并且温压压制曲线与 室温压制曲线具有大致平行的走向,如图2所示。但据此认为温压过程中并未出现新的致密化机制,理由并不充分。因为聚合物在其玻璃化温度以上和以下时具有明显不同的润滑效果,并且,这种效果会随着压力的增大而变差[26-27]。同时,温度和压力对粉末材料可塑性的影响也不是线性关系。至于温压压制曲线与室温压制曲线为什么会具有大致平行的走向,尚需进一步研究。 图2 温压工艺与传统压制工艺生坯密度之比较[5] 4 温压技术的技术关键 温压技术的技术关键主要有两点,一是预制粉末和新型润滑剂,二是温压系统。在Ancorden se温压工艺中使用的是Ancordense预制粉末,它是在生产预制粉末的Ancorbond工艺的基础上,采用一种新型的聚合物粘结剂而开发出来的。然后在预制粉末中添加新型高温聚合物润滑剂,并在粘结剂的玻璃化温度以上进行压制。类似的预制粉末还有瑞典Hoeganaes AB公司的Densmix[13-14]和加拿大QAuebec Metal Powders公司的FLOMET WP[13] 等。 在开发温压技术时首要的任务就是选择或研制出适当的聚合物添加剂(包括粘结剂和润滑剂)。但由于聚合物的物理性能,特别是其在粘流态时的粘结性能和润滑性能,不仅与其单体种 类有关,而且还随其聚合度以及构型与构象的不同而变化,同时,聚合物在温压工艺中的作用还存在很多争论,因此,温压工艺中聚合物的确定存在相当的困难。一般说来,所选聚合物应具有以下特点:(1)较低的玻璃化温度(如150℃左右),否则会给制备工艺带来困难;(2)易溶于挥发性溶剂;(3)易于在合金粉末表面形成润滑膜或在压制过程中形成转移膜,即两者间的润湿性好;(4)裂解时应比较缓和、平稳,避免瞬间产生大量气体,导致在粉冶件中产生新的空洞;(5)能阻止或减缓合金粉末氧化,由于铁粉等合金粉末在温度超过90℃以后氧化速度明显加快,因此这一性能尤为重要。据文献[19]报导,添加有润滑剂的混合粉 在150℃保温2小时后,氧含量仅由0.470%增加到0.477%;(6)能为人体和环境所接受。 据有关文献[9-11,16,27]报道,这种添加剂大致可从下列有机物中选取或进行组 合和改性;聚酰胺、聚酰亚胺、聚醚亚胺、聚碳酸酯、聚甲基丙烯酸酯、聚醚、聚苯撑醚、聚矾、纤维素酯、热塑性酚醛树脂、聚乙二醇、阿克蜡、甘油等。 聚合物的加入方式主要有三种:(1)将聚合物粉末与合金粉末干混;(2)在聚合物融化温度以 上将两者进行混合;(3)将聚合物溶入易挥发的溶剂中后与合金粉末湿混。方法(1)需用粒度很小的聚合物粉末,但聚合物一般很难破碎,而粉末太粗时其作用难以完全发挥。后两种方法则是为了在合金粉末表层涂敷一层均匀的聚合物薄膜,这一方面可使聚合物分散均匀,更好地发挥聚合物的润滑作用,另一方面聚合物薄膜能阻止合金粉末在高温下氧化。但方法(2)工艺复杂,故通常采用方法(3)进行混料。 图3 MW-6粉末加热输送系统结构原理图 温压系统主要是指粉末预热输送系统和阴模加热装置。一般说来,快速而均匀的加热系统( 可减少粉末的氧化)、稳定且均匀的粉末温度、粉末的精确输送及送粉是这类温压系统的共 同要求。美国Hoeganaes公司与压机生产厂家Cincinnati公司和Gasbarre Products公司密切 合作,开发温压新技术,研制用于温压生产的设备。Gasbarre Products公司研制出了MW-6 型预热粉末输送系统,其结构原理如图3所示[2,29]。该系统的最大特点是采用微 波加热,因而加热速度快,可大大减缓混合粉末的氧化,并且适应性强。在该系统中,混合 粉末经输入料斗进入微波室加热,然后被送至输出料斗,经软管到送粉靴,最后到达阴模。整个系统采用程序闭路控制,通过改变微波功率与粉末输送速率可控制微波室及混合粉末的加热温度。输出料斗、软管及阴模等都要加热到规定的温度范围。阴模采用电阻式加热器加热,并将一热电偶嵌入阴模中以控制温度,全部模具应处于均一温度状态,以免由于温度不均而导致模具部件不匹配。同时还必须注意应将阴模传递给压机机架的热量减小到最低程度,以免损坏压机。 开展温压技术的研究,不仅有利于粉末冶金工业的发展,对粉末冶金成形理论的研究也具有 十分重要的意义。为此,作者提出以下的建议: (1)研制粘结剂和润滑剂,并开发出适用的预制粉末; (2)开展温压压制理论及温压过程计算机模拟方面的研究工作; (3)探讨温压件的烧结机制; (4)研究后续热处理对温压粉冶件的影响; (5)运用温压技术制备铁基复合材料。 基金项目:教育部重点科技攻关项目(9782);教育部科技项目(97118) 作者简介:张双益,男,华南理工大学博士研究生 作者单位:华南理工大学,广州 510641
出处: 材料科学与工程
版权与免责声明:
① 凡本网注明"来源:中国粉体网"的所有作品,版权均属于中国粉体网,未经本网授权不得转载、摘编或利用其它方式使用。已获本网授权的作品,应在授权范围内使用,并注明"来源:中国粉体网"。违者本网将追究相关法律责任。
② 本网凡注明"来源:xxx(非本网)"的作品,均转载自其它媒体,转载目的在于传递更多信息,并不代表本网赞同其观点和对其真实性负责,且不承担此类作品侵权行为的直接责任及连带责任。如其他媒体、网站或个人从本网下载使用,必须保留本网注明的"稿件来源",并自负版权等法律责任。
③ 如涉及作品内容、版权等问题,请在作品发表之日起两周内与本网联系,否则视为放弃相关权利。